The factors of underwater cutter damage and the solutions
The factors of underwater cutter damage and improvement solutions are here!
In actual production, the underwater pelletizing equipment is prone to cutter damage, resulting in unqualified pellets, which not only increases the cost of cutter replacement, but also may cause customer quality complaints and economic losses.
Extending the service life of the cutter can not only ensure the appearance quality of granulation, but also save the material cost of the cutter, and at the same time reduce the number of stops of the extruder caused by the replacement of the cutter. Therefore, it is very necessary to study the factors affecting the service life of the cutter.
What is the cutter damage?
In long-term continuous production, different forms of cutter damage will occur, including cutter wear, cutter passivation and deformation, cutter breakage, etc. Among them, during normal production, the wear and passivation of the cutter is the most common phenomenon; when the production fluctuates, the cutter is prone to entanglement (see Figure 1), and cleaning the resin covering the cutter is easy to passivate and deform the blade . In order to prolong the service life of the cutter, special attention should be paid to the wear and tear of the cutter and the phenomenon of material sticking to the knife.
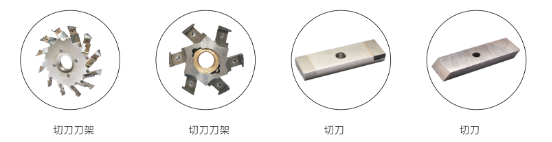
Influencing factors of cutter damage
1,Pelletizing process
The contact pressure of the cutter is regulated by the feeding air pressure and the returning air pressure. The feeding air pressure increases and the returning air pressure decreases. The closer the contact between the cutter and the die plate, the greater the friction between the cutter and the die plate, resulting in an increase in the current of the cutter and an increase in the wear of the cutter.
In addition, when the extruder is started, in order to make the cutter and the die plate closely contact without generating padding material, the initial feeding air pressure is set to 0.6 MPa in manual mode, and then the feeding air pressure is reduced by 0.01 MPa each time until when the feeding air pressure is 0.48 MPa, the automatic mode is enabled; during the process, the maximum current of the cutter is as high as 206A, which is about 30A higher than the normal value (see Figure 2).
When the rotation speed of the cutter increases, the force of the pelletizing water on the cutter to press the die plate increases (its effect is equivalent to increasing the feeding air pressure), and the number of frictions between the cutter and the die plate per unit time increases, so the cutter wears faster. It should be noted that when the cutter speed is too high, the cutter speed becomes the main factor affecting the cutter current. The cutter current increases obviously (see Table 1).
- PP Grade
For different grades of PP, the physical properties are quite different. In general, the lower the MFR of PP, the greater the hardness of the molten material, the greater the friction on the cutting edge, and it is easier to passivate the cutting knife. In actual production, grade switching is often carried out according to market demand, and transition materials will be generated during the process of grade switching.
The MFR of the transition material continues to change, so the pelletizing process (water temperature, die plate temperature and barrel temperature, etc.) needs to be adjusted accordingly, so that the hardness change of the transition material passing through the barrel and the die plate is uncertain. Due to the change of the hardness of the transition material, the cutter is subjected to repeated action of alternating stress, resulting in passivation of the cutter.
- Polymerization/Modification Process
For the same grade of PP, the MFR fluctuates within a certain range due to the characteristics of the polymerization/modification process. When the MFR fluctuates greatly, it is also unfavorable to prolong the life of the cutter. In actual production, due to the influence of changes in process and raw materials, such as fluctuations in the amount of additives added, inconsistent feeding, uneven catalyst preparation, and low purity of raw materials, the uniformity and stability of product properties may be affected, which is not conducive to Knife protection during granulation.
The fluctuation of the post-processing section of PP polymerization can also have an adverse effect on the properties of the powder. For example, due to the fluctuation of the steam in the drying unit of the polymer raw material, the drying effect is not good, so that the raw material contains a certain amount of water, and finally the knife wrapping phenomenon occurs in the pelletizer.
- Others
Equipment factors include the flatness of the cutter plate, the perpendicularity of the cutter shaft and the die plate, the flatness of the cutter surface and the material of the cutter.
Improvement solutions
- Granulation process
During production, the feeding air pressure and the returning air pressure should be kept stable to avoid fluctuations. In order to ensure the quality of pelletize, sometimes need to maintain the feed air pressure, and when the cutter current is large, the retract air pressure can be slightly increased to reduce the cutter wear; it should be noted that the retract air pressure should not be too high Large, so as to avoid normal dicing when the production process fluctuates, which will eventually lead to the occurrence of knife padding and material sticking to the knife.
In the process, high feeding air pressure can increase the wear of the cutter, so frequent starting and stopping of the extruder should be avoided; At the same time, in the process of switching from manual mode to automatic mode, the feeding air pressure should be gradually reduced. If the setting value of the feeding air pressure drops suddenly, the adhesion force of the cutting knife to the die plate is instantly reduced, and more molten material is easy to punch out of the die plate, which can lead to padding and material sticking to the knife. At the same time, the cutting knife and the die plate must be coated with silicone oil before processing, so that the molten material sticking to the knife can be thrown away from the knife in time.
- Material Grade
When granulating materials of the same grade, it is necessary to comprehensively adjust the temperature of the cutting water, die plate and the barrel to find the best combination of the three, so that the molten material has a suitable pelletizing hardness. In this way, the phenomenon of knife padding and material sticking to the knife caused by a large amount of molten material quickly punching out of the die plate can be avoided.
When changing the material, it is necessary to adjust the temperature of the cutting water, die plate and barrel according to the MFR trends, so that the molten material has a suitable hardness for cutting, to ensure a good appearance of the pellets. If there is tailing material, snake skin material, etc., it is necessary to adjust the granulation process in time according to the actual situation to avoid the occurrence of padding knife and material sticking to the knife (Table 2).
- Process stability
Control the stability of front-end processes and equipment to ensure stable physical properties produced with the same formula, such as reducing feed fluctuations and adverse effects caused by uneven dispersion of additives and pigments, ensuring the purity of raw materials and keeping physical properties within a narrow range keep it steady.
Minimize the replacement of materials with a large MFR span, and optimize the modification process to reduce the generation of transition materials, so that they can quickly enter the qualified production stage, thereby reducing the adjustment time of the pelletizing process in the production of transition materials, which is conducive to cutter protection. In addition, ensure the normal operation of the material processing section and avoid wide fluctuations in the moisture content of the material.
- Others
It is very important to ensure the installation accuracy of the cutter. The flatness of the cutter disc should be less than or equal to 0.01 mm, the perpendicularity of the cutter shaft to the template and the flatness of the cutter surface should be less than or equal to 0.03 mm.
By sharpening the knife, the flatness of the cutting disc, the perpendicularity between the cutting shaft and the template, and the flatness of the cutting surface can be improved to match the template. Therefore, the quality of the sharpening should be improved, and the feed air pressure should be reasonably controlled. and sharpening time to avoid knife damage during sharpening.
The material selection of the cutter is also very important. The hardness of the cutter should be lower than the hardness of the template to avoid the cutter from scratching the template. If the cutter frequently breaks, other high-quality cutters can be used or the cutter can be re-heated to eliminate the cutter. Defects in the texture of the material.
Regularly check the pH value of the pelletizing water. When the pH value is less than 7, open the fresh and refined water replenishment valve to make the pellet water overflow, so that the pelletizing water pH value is qualified, and other water such as industrial water shall not be added to the pelletizing water tank.